With the improvement of automation, direct manual monitor and interference on production is fading so as to assure the uniformity of product quality, and the importance of sensors is becoming more and more apparent.
For sensor technology, the requirements are not limited simply in mechanical and rough monitor, but especially to the reliability and stability of inspection, as well as simplification of installation and debugging, compact size and multiple application. However, the complexity and variability of level measurement environment make it challenging for sensor application. Now let’s talk thoroughly about level measurement methods of model selection of ultrasonic sensors.
Level Measurement Method with Ultrasonic Sensors
Ultrasonic sensor is a commonly used type which produce a mechanical wave with higher vibration frequency than sound wave. The wave is generated by voltage stimulated vibration of transduction chip. It is able to obtain high frequency, short wavelength and little diffraction. With excellent orientation, it can transfer as radiation and perform directional communication. Ultrasonic wave has advantages in penetrating liquid and solid, especially in non-transparent solid, in which the wave can go through a depth of dozens of meters. Ultrasonic wave would generate apparent reflection echo when reach any impurities or interface, and generate doppler effect when reach active objects.
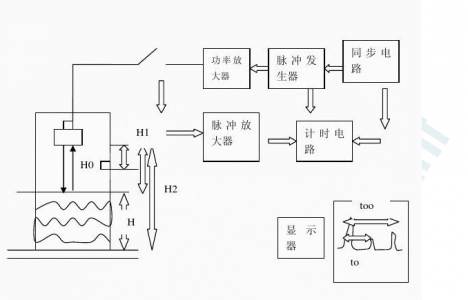
The ultrasonic sensor adopted by the system works in a frequency of 40kHz. Emission sensor sends an ultrasonic pulse, which reaches the fluid level and then be reflected to the receiving sensor. Measure the time from the pulse is sent to it is received, so that the distance between the sensor and level can be calculated with the sound velocity in the certain medium, and then the fluid level can be confirmed. Considering ambient temperature’s influence on ultrasonic wave velocity, temperature compensation is applied to enhance measurement accuracy. The calculation formula is:
V=331.5+0.607T (1)
In which: V is ultrasonic wave velocity in the air; and T is ambient temperature.
S=V ×t/2=V×(t1-t0)/2 (2)
In which: S is measured distance; t is the time difference between sending and receiving ultrasonic pulse; t1 is the moment that ultrasonic echo is received; t0 is the moment that ultrasonic pulse is sent.
By capture function of MCU, t0 and t1 can be easily measured, and then measured distance S can be obtained by programmed software via the formulas above. Since that the MCU of this system adopts mix signal processor which featured SOC and internally integrated temperature sensor, it can conveniently realize temperature compensation to the sensor via software.
To Select an Ideal Level Measurement Sensor
Liquid level sensors are used in many industries for process control. Before selecting a level sensor, there are several questions to be considered: is it liquid or solid to be measured? What’s the ambient temperature and pressure? Is point level measurement or continuous measurement required? How large should the measurement range be? Is the measured material conductive? Would the material cover or be piled on some surface? Would the liquid surface generates turbulence, foam or steam? Is contact-type or non-contact type required? What kind of output is needed, analog, relay, digital display or else? It’s significant for selecting an ideal sensor to get familiar with operation principal, advantages and disadvantages of level sensors. Followings are the measurement principals of commonly used level sensors.
The operation principal of Ultrasonic level sensor is to detect the time difference between sending and receiving ultrasonic wave for calculating level height. The sensor is flexible and easy to install, but is also vulnerable to energy loss, thus it is not suitable for wave-absorbing environment such as foam, dust and steam, etc. We ISweek recommend SENIX ultrasonic level sensor from the USA – ToughSonic-50.

The maximum range of ToughSonic-50s ultrasonic sensor is 50 feet (15.2m). Same as all ductile sensors, it is durable and convenient enough for tough environment. Moreover, ToughSonic 50s can endure complete immersion, corrosion and surge. ToughSonic 50s can adopt 3 different housings which are all equipped with RS-232 or RS-485 serial interface. These 9-wire sensors allows 6 serial, analog and / or switched output simultaneously. They can also be completely configured via SenixVIEW software. The main sensors are widely used in remote level applications and tough factory conditions. They are also widely applied in realms like level or height measurement, remote level measurement, distance-proximity detection, object detection and factory automation, etc.
Photoelectric level sensor is a new measuring and control device of point liquid level, which uses the principal of light’s reflection and refraction when passing through different medium interface. Photoelectric level sensors are of simple structure and high positional accuracy with no mechanical parts and no need of debugging. They are of low power consumption and small size with high sensitivity and corrosion resistance. They have strong chemical property so that they can endure high temperature, high pressure and strong corrosion, and resist the influence from medium to be tested. On liquid level measurement, ISweek recommends low cost SST Liquid Level Sensors– LLC200A3SH.

LLC low-cost level sensors series provides single-point level measurement. IR emitter and detector are included in special design for mass OEM order, which are installed at accurate positions that ensure them to achieve good optical coupling in the air. When the conical end of the sensor is immersed in any liquid, the infrared light will transmit through the conical surface so that the light intensity reching the detector will be weakened. This kind of sensors are mainly applied in realms like hot spring pool, liquid leakage detection, drink vending machine, beverage dispenser, medical treatment, compressor, printer, water pump, household appliances, oil level monitor, HVAC, machine tool, H-L level switch, water level control and automotive electronics, etc.
After getting understand the working principals of various level sensors, and based on the property and status of liquid to be tested, we can choose the level sensor that serves us best.
Thanks a bunch for sharing this with all of us you really know what you are talking about! Bookmarked. Kindly also visit my website =). We could have a link exchange arrangement between us!